Third Hand Upgrade

Author: Rodolfo Antonio Salido Benítez
Completion Date: Sep 16, 2018
Software: Autodesk Fusion 360, PhotoScanPro, MeshLab, Simplify 3D
Place of Creation:Biomedical Research Facility II. (UCSD)
Techniques: Photogrammetry, geometric modeling, organic modeling, computer aided design & manufacturing, rapid prototyping, and additive manufacturing.
Materials: Polylactic Acid (PLA), Printed Circuit Boards (PCB's), Arduino micro-controller, servo motors, proximity sensor, cable tensioners, aluminum extrusion, and lithium battery.
Description
The Third Hand Upgrade is a biomimetic prosthetic augmentation attachment designed to serve as an additional limb. The project consists of an open-source 3D printed prosthetic hand, developed by exiii under the name HACKberry, mounted on an aluminum pylon with biomimetic fairings. It interfaces with my right forearm through a mount with micro-adjustable tensioners and an adjustable elbow joint. The prosthetic hand's thumb opposition, pinch-release, and power grasp movements are mediated by three servo motors controlled by an Arduino microcontroller. This system translates muscle movements, sensed by an infrared proximity sensor, into open and close hand commands. All plastic components were printed in PLA using a personally fabricated RepRap 3D printer.
The HACKberry design uses two motors to control finger movements: one for the index finger and another for the middle, ring, and pinky fingers. A third motor controls thumb opposition, toggled by a button on the back of the hand. Another button locks the non-index fingers, enabling exclusive control of the index finger for pinch movements. The back of the hand also features an on/off switch and a calibration button.

Inspiration
This project was influenced by the cooperative design surrounding prosthetics, artistic ideas of technological body augmentation, and access to CAD and manufacturing technologies. Globally distributed maker communities, such as e-NABLE and mission arm Japan, have built platforms for connectivity between volunteers and individuals needing mobility assistive devices since 2014 and 2015, respectively. These communities develop engineering solutions for upper limb mobility needs through cooperation rather than competition. Their open-source designs, often licensed under Creative Commons, are available in online 3D model repositories. This allows anyone with access to additive manufacturing technologies to replicate them, and individuals with engineering expertise to contribute to their development. These platforms encourage individuals to work for non-monetary rewards, an idea that resonates with me and drives my active participation in developing prosthetic devices.
Since my first exposure to these cooperative projects, I have researched and implemented additive manufacturing techniques coupled with CAD to develop a custom interface between an external mechanical device and my body. I focused on developing and documenting accessible 3D scanning techniques to inform maker communities of cost-effective methods for high-fidelity socket design. I dedicated an academic quarter to a self-funded undergraduate research project on prosthetic socket design, conducting literature reviews and evaluating a new commercial 3D scanning product, Scanify by Fuel3D. Although the product proved unfit for prosthetic applications, the core photogrammetric 3D scanning technology was further explored and implemented in the project's final product.
"A prosthesis not as a sign of lack, but rather a symptom of excess."

The project was envisioned as a body augmentation rather than a rehabilitative prosthetics project, as a tribute to the influential work of Australian performance artist Stelarc. Stelarc has been a prominent voice in the discourse on the limitations and potential technological evolution of the human body since 1980. This project alludes to his Third Hand performances, showcasing the potential of symbiotic relationships with computerized systems, mechanical body redesign, and technology-mediated human evolution.
Unlike Stelarc's Third Hand, built with assistance from Imasen in Nagoya, Japan, this project was partially designed and fully manufactured by the end user—myself—using easily sourced materials and widely distributable technologies. Thus, it is not an exaggeration to state that technologically directed evolution is at our doorstep. The body augmentations designed by scientists and artists can be practically reproduced, adopted, and enhanced through global cooperation.
Methods
A HACKberry hand was 3D printed and constructed following the project's documentation, then attached to a biomimetic artificial forearm that interfaces with a biological limb through a personalized adjustable mount. The biomimetic forearm was designed to mirror the biological limb and the adjustable mount was designed around a 3D scan of the same limb.
Photogrammetric 3D scan
A 3D mesh of my arm was generated through dense point cloud reconstruction from 29 individual photos taken approximately 10º apart. To decrease surface uniformity of the skin, a temporary pattern of X's, spaced one inch apart, was transferred to my arm using tattoo stenciling ink. This pattern improved the performance of the dense point cloud reconstruction algorithm by providing recognizable anchor points. The photos were imported into PhotoScanPro, and the camera positions in 3D space were inferred by aligning the photos using the Align Photos workflow. A dense point cloud was then generated using the Build Dense Cloud workflow. Finally, the 3D mesh was constructed using the Build Mesh workflow.
The model was exported and the mesh complexity was decimated using MeshLab to achieve a smoother surface finish while preserving overall topology.

Organic Sculpting (CAD)
The 3D scan was imported into Autodesk Fusion 360 to serve as a mold for the organic design of cosmetic fairings and the forearm mount. In the sculpting environment of Fusion 360, T-Spline planes were created for each component. The Pull feature was used to align the vertices of the planes with those of the imported mesh. Faces and vertices of the T-Spline planes were then modified to achieve a satisfactory cosmetic product with high geometric fidelity to the biological limb. An adjustable elbow was sculpted using a Quadball T-Spline shape.The following videos can serve as a guide to the aforementioned processes: Modeling for the human body in fusion 360 and Mesh modeling.
Geometric Modeling (CAD)
The modeling environment was used to design mechanical components needed to attach the HACKberry hand and cosmetic fairings to the aluminum pylon, including a functional adjustable elbow joint based on a spring-loaded locking mechanism and mechanical mounts for the micro-adjustable tensioner system sourced from Boa (BOA S2-S). The slotted grills of the fairings were designed to allow tool access to the aluminum pylon, reduce component weight, and enhance cosmetics.
Additive Manufacturing (CAM)
AAll 3D printed components were manufactured on a RepRap Kossel 3D printer using PLA. All models were sliced using Simplify 3D at a 200-micron layer resolution, printed with supports and a raft. HACKberry hand components were downloaded from this repository.

Results
The final product is a prosthetic augmentation attachment with a micro-adjustable limb interface, an adjustable elbow joint, adjustable wrist rotation, ulnar and radial deviations, an opposable thumb, and lockable non-index fingers. The device was intended to be controlled by the same arm it was mounted on, but the device's weight caused sensor noise, making accurate control impossible. Consequently, the sensor was mounted on the opposite arm. Further development will explore myoelectric control through pectoral muscle contractions.
A button on the back of the hand activates an 8-second calibration procedure. During this time, the user contracts and relaxes the forearm muscles near the sensor, and the minimum and maximum sensor readings are stored. The range between these values is reassigned to a scale of 0-100, with values below 15 resulting in finger extension, values around 25 holding the finger position, and values above 40 causing finger contraction with variable speed.
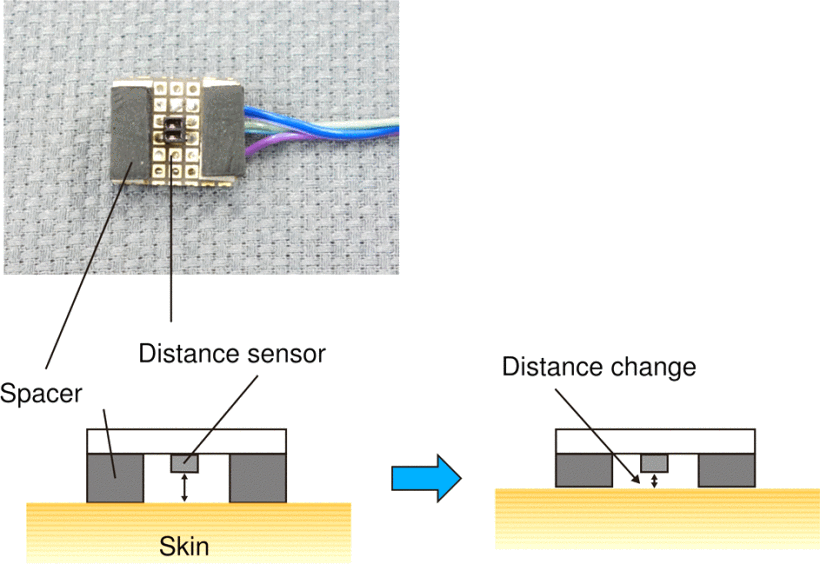
The sensor measures changes in the distance to the skin it is mounted next to. When muscles contract, the surrounding cushions compress, decreasing the distance between the sensor and the skin. This sensing system has proven to be an effective linear actuator for prosthetic device control, as demonstrated by Masahiro Yoshikawa et al. in their paper Trans-radial prosthesis with three opposed fingers
Rotational adjustments are made by pressing spring-loaded buttons around the device. Thumb opposition is activated by pressing a button on the back of the hand, toggling the thumb motor between opposed to the index finger or in the plane of the palm. Another button locks the non-index fingers in their current position, allowing isolated index finger movements for pinching gestures. These features enable the hand to grasp irregular objects.
Limitations
The Third Hand Upgrade has several limitations. The device's weight on my forearm caused significant shear stress, necessitating a textile elbow compression sleeve as an interface material. This reduced discomfort, but extending the mount design to the bicep for weight bearing is necessary. Controlling the device with the same arm was impossible due to weight-bearing forces, so the opposite forearm was used, limiting two biological limbs to control the artificial limb. Constant use of the analog motors generates enough heat to trip resettable fuses, causing the motors to malfunction after 15 minutes of use. Cooling the motors resolves this issue, but it is a significant limitation for practical use.
Future Development
Future development will explore the use of myoelectric sensors to control the Third Hand Upgrade using pectoral muscle contractions for open and close hand commands. Encoding thumb opposition and non-index finger lock commands as muscle contractions will allow more fluid control of the artificial limb. The mount will be redesigned to extend toward the bicep to distribute the device's weight and prevent excessive torsion forces on the forearm.
Ultimately, I aim to fit the HACKberry prosthetic hand to an individual with upper limb mobility needs. This project was essentially a pilot study to determine the feasibility of using photogrammetry and CAD to manufacture a prosthetic socket. I believe I have acquired the necessary skills to achieve this goal and will
Acknowledgements
I want to express deep gratitude to the exiii team for placing their trust in the open source community to push their project forward, especially to Hiroshi Yamaura for his constant engagement in the HACKberry forum. I would also like to acknowledge Greg Humphrey for putting up with countless hours of 3D printing noise, and Satima Anankitpaiboon for her help with hardware sourcing and her technical support.